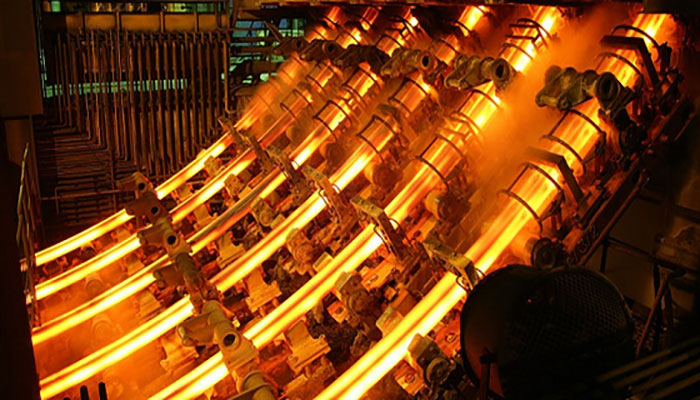
فرق شمش قوس الکتریکی و کوره القایی
در حال حاضر برای تولید فولاد روش های مختلفی وجود دارد که از جمله آن می توان به دو روش استفاده از کوره ذوب قوس الکتریکی و کوره ذوب القایی اشاره کرد.
در کوره قوس الکتریکی آهن قراضه (فولاد) با استفاده از یک قوس الکتریکی گرم می شود. اساس کار این کوره ها به این صورت است که فولاد به درون کوره ریخته شده و الکترودها باعث ایجاد حرارت و انجام عملیات ذوب می شود.
کوره القایی گرمایش القایی به روش القای انرژی الکتریکی است که در سال 1990 میلادی مورد استفاده قرار گرفت. گرمایش القایی به این صورت انجام می شود که اسیلاتور جریان متناوبی را به کویل اعمال می کند که در نتیجه میدان مغناطیسی متناوبی در کویل ایجاد می شود. با توجه به اینکه جنس مواد موجود برای گرمایش، رسانا هستند، جریانی درون مواد القا می شود که باعث ایجاد گرمایش درون مواد رسانا می گردد.
هر چند در هر دو روش شمش های القایی تولید می شوند اما در توانایی تصفیه، مصرف برق، بازده عناصر آلیاژ، شرایط ترمودینامیکی و بکارگیری نیروی انسانی و دفع گرد و غبار و در بهره برداری تفاوت هایی وجود دارد که در این مقاله به آن پرداخته می شود.

تفاوت شمش قوس الکتریکی و کوره القایی در توانایی تصفیه
تفاوت شمش قوس الکتریکی و کوره القایی در توانایی تصفیه را می توان به صورت زیر شمرد:
- با توجه به اینکه سرباره قوس الکتریکی گرم است در نتیجه در رفع اکسیداسیون نسبت به کوره القایی قوی تر است و فسفر و گوگرد را سریع تر حذف می کند.
- با توجه به اینکه فسفر زدایی و گوگرد زدایی در شرایط مختلف (دمای بالا و پایین مذاب) انجام می شود در صورت بالا بودن دو عنصر پایین آوردن میزان آن ها در روش القایی دشوار است.
- با توجه به اینکه مولکول های آمونیاک در بخش دارای دمای بالای قوس به اتم ها یونیزه شده و توسط مایع مس جذب می شوند در نتیجه محتوای کلر کوره قوس الکتریکی بیشتر از کوره القایی است.
- با توجه به اینکه سرباره کوره القایی سرد است محتوای نیتروژن آن کمتر از قوس الکتریکی و محتوای اکسیژن آن بیشتر از قوس الکتریکی است. در نتیجه اکسیژن در کوره القایی به خوبی کنترل نمی شود و در نتیجه فرو آلیاژ ایجاد می شود.
- در کوره القایی از کربن خالص به صورت گرافیت برای کربن دهی استفاده می شود در نتیجه در این روش برای ذوب بار فلز حتما به کربن دهی نیاز است در صورتی که در کوره قوس الکتریکی با یک الکترود سنگی این عملیات انجام می شود.
تفاوت شمش قوس الکتریکی و کوره القایی در بازدهی عناصر آلیاژ
سرباره در قوس الکتریکی گرم است در نتیجه زمانی که این کوره در حال کار است عناصر آلیاژی موجود در مواد اولیه سرباره اکسید خواهند شد و بعد از سرباره به فولاد مذاب بازگردانده خواهند شد. در نتیجه سوختن عناصر آلیاژی در کوره قوس الکتریکی بیشتر از کوره القایی است و از این رو بازدهی عناصر آلیاژی در کوره های القایی بیشتر از کوره های قوس الکتریکی است. هر چند در عملیات کوره القایی از کاربید سیلسیم پرعیار برای تنظیم ترکیب شیمیایی استفاده می شود در نتیجه هزینه آلیاژها و مواد افزودنی غیرفلزی در دو فرآیند متفاوت است. از این رو با توجه به اینکه کیفیت ذوب در کوره قوس الکتریکی بالا است لذا فرآیند آلیاژ سازی به خوبی و با کیفیت بالا انجام می شود به طوریکه این کوره آلیاژهای نسوز را تحت تاثیر حرارت ذوب می کند. از این نوع از کوره حتی برای بازیافت ضایعات فلزی از قبیل آلومینیوم نیز می توان استفاده کرد.

تفاوت شمش قوس الکتریکی و کوره القایی در مصرف برق
در کوره القایی نیاز به مصرف برق و انرژی بالاتر از قوس الکتریکی است. زیرا در کوره قوس الکتریکی ورود انرژی الکتریکی بالاتر همراه با جریان بالاتر الکترود و در نتیجه نیاز به مصرف انرژی کمتر است. همچنین با ورود انرژی شیمیایی با اکسیژن مافوق صوت و تزریق کربن زمان روشن بودن کوره نسبت به کوره القایی کمتر و در نتیجه مصرف برق آن پایین تر است.
تفاوت شمش قوس الکتریکی و کوره القایی در شرایط ترمودینامیکی
در کوره القایی دما و حرارت، قدرت هم زدن، زمان تصفیه و حفظ درجه حرارت ثابت نسبت به کوره قوس الکتریکی راحت تر است. یکی از دلایل این امر شرایط ترمودینامیکی و جنبشی در کوره القایی است که باعث همگن سازی مواد مذاب و ترکیب بهتر فولاد می شود.
تفاوت شمش قوس الکتریکی و کوره القایی در نیروی انسانی
بکارگیری نیروی انسانی در کارگاه قوس الکتریکی و کوره القایی تقریبا برابر است. در تولید شمش قوس الکتریکی حداقل چهار نفر و در کارگاه کوره القایی در مجموع پنج نفر در عملیات ساخت مورد نیاز است
تفاوت شمش قوس الکتریکی و کوره القایی در دفع گرد و غبار
گرد و غبار ایجاد شده از کوره قوس الکتریکی به طور مجدد مورد استفاده قرار می گیرد و ارزش تجاری دارد و مقدار گردو غبار بعبارتی باطله کوره القایی فراکنس متوسط، به میزان یک درصد و نسبت به کوره قوس الکتریکی کمتر است.
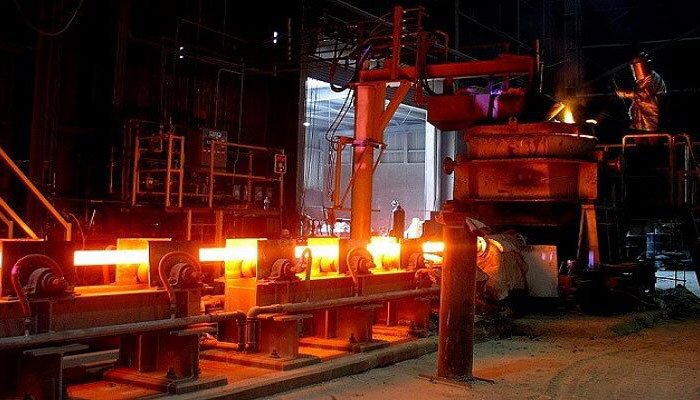
تفاوت شمش قوس الکتریکی و کوره القایی در بهره برداری
سوختن عناصر آلیاژی در کوره قوس الکتریکی بیشتر از کوره القایی و کیفیت ذوب در کوره قوس الکتریکی بالا است از این رو فرآیند آلیاژ سازی باکیفیت بالا انجام می شود به طوریکه این کوره آلیاژهای نسوز را تحت تاثیر حرارت ذوب می کند. لذا از نظر بهره برداری با توجه به اینکه در کوره قوس الکتریکی الیاژهای نسوز هم ذوب می شود شمش های ایجاد شده دارای ناخالصی بیشتری هستند. هر چند زمان ذوب در این کوره خیلی کمتر از کوره القایی است.
سایر تفاوت های شمش قوس الکتریکی و کوره القایی
- در کوره های القایی عملیات ذوب شدن با سرو صدای کمتری نسبت به قوس الکتریکی انجام می شود.
- با توجه به اینکه در کوره القایی نیاز به گرمایش مضاعف در هر چرخه نیست لذا شروع و پایان عملیات سریع انجام می شود.
- در کوره قوس الکتریکی دمای کوره و درجه حرارت فولاد مذاب به مدت زمان طولانی مورد کنترل قرار می گیرد.
- در ذوب قراضه ها با استفاده قوس الکتریکی کیفیت فولاد تحت تاثیر آلیاژهای مختلف قرار می گیرد در نتیجه در این روش ناخالصی بیشتری وجود دارد.