تولید فولاد با کوره القایی
کوره های القایی برای چندین دهه در صنعت فولاد استفاده میشود و در حال حاضر یکی از محبوبترین وسایل ذوب و نگهداری مواد آهنی میباشند. کوره القایی نوعی کوره ذوب الکترونیکی است که از جریان الکتریکی برای ذوب فلز استفاده میکند. عبور جریان از یک سیم پیچ و استفاده از میدان مغناطیسی برای ایجاد جریان در هسته سیم پیچ، اساس کار کوره های القایی را تشکیل میدهد. در این کوره ها از حرارت ایجاد شده توسط تلفات فوکو و هیسترزیس برای ذوب فلزات یا هرگونه عملیات حرارتی استفاده میشود. در ادامه با توضیح مختصری از توسعه کوره های القایی در دنیا و تشریح تولید گرما به روش القا به معرفی انواع کوره القایی و تولید فولاد با کوره القایی پرداخته میشود.
مختصری از توسعه کوره القایی
فوکو در سال 1863 در مقاله ای تحت عنوان القا در جریان هسته نظری های راجع به جریان فوکو ارائه داد و در رابطه با انتقال انرژی از یک کویل به یک هسته توپر بحث نمود و در اواخر قرن نوزدهم استفاده از تلفات فوکو و هیسترزیس به عنوان منبع گرمایش القائی از طرف مهندسین مطرح شد و در سال 1890 اولین کوره القایی برای ذوب فلزات توسط ادوارد آلن ساخته شد. اولین تولید فولاد با کوره القایی در سال 1907 در آمریکا به دست آمد و در سال 1906 اولین کوره القایی که با جریان سه فاز کار می کرد، در آلمان ساخته شد و امروزه با پیشرفت و رشد تکنولوژی انواع کوره های القایی برای ذوب انواع فلزات به کار می رود.
تشریح تولید گرما از الکتریسته به روش القا در تولید فولاد
کوره های القایی حرارت خود را بدون احتراق و به صورت پاک ایجاد میکنند. جریان الکتریکی متناوب از مولد برق که میتواند مستقیما از شبکه یا یک مولد محلی و یا یک مبدل فرکانسی به یک کوره و از طریق یک سیم پیچ (اکثرا ساخته شده از لوله های مسی توخالی) جریان می یابد. که این جریان باعث ایجاد یک میدان الکترومغناطیسی درمحل مورد نظر میگردد و این میدان از شارژ فلز رسانا میگذرد که موجب تولید یک جریان بسیار زیاد و همچنین تلفات زیاد در آن فلز رسانا میگردد.
میدان مغناطیسی حول سیم پیچ و مسیر
در واقع میتوان تصور کرد که کوره القایی یک ترانسفورماتور است که در ثانیه چندین برابر جریان اولیه خواهد شد. در کوره القایی جریان در یک جهت در سیم پیچ القایی باعث جریان در جهت مخالف در فلز میشود.
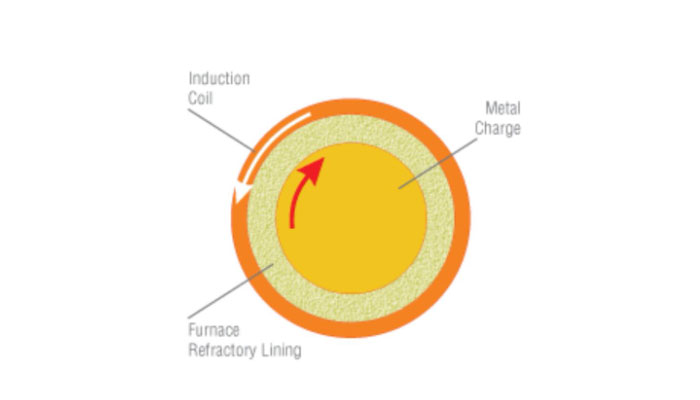
عملکرد کوره های القایی
از کوره های القایی برای ذوب کردن، چدن، فولاد، مس، آلومینیوم و فلزات گرانب ها استفاده میشود. ذوب فلزات در کوره القایی شامل قراضه انتخاب شده با کربن مشخص است. قراضه در محفظه ای استوانه ای از مواد نسوز (بوته) قرار می گیرد که توسط یک سیم پیچ القایی خنک شونده با آب احاطه شده است. جریان متناوب با فرکانس بالا از سیم پیچ عبور می کند و باعث ایجاد میدان مغناطیسی متناوب در داخل مذاب می شود که گرمای شدیدی تولید میکند و همچنین دارای اثر همزنی هم میباشد نه تنها دستیابی به دمای بالا ممکن است، بلکه کنترل دقیق دما هم امکان پذیر می باشد.
اساس کار تولید فولاد با کوره القایی براصل القا میدان مغناطیسی مبتنی میباشد. نحوه عملکرد به این صورت است که ابتدا با استفاده از جریان برق شهر و بوسیله مبدل، فرکانس جریان نسبتا زیادی بیش از ۱۰۰۰ آمپر) با فرکانس ۳۰۰ تا ۱۰۰۰۰ هرتز ساخته می شود در کوره های فرکانس بالا بیش از ۱۰۰ کیلوهرتز میباشد) سپس این جریان به سیم پیچ ،کوره اینداکتور یا کویل اعمال شده و با عبور از آن باعث ایجاد میدان مغناطیسی با همان فرکانس در وسط کویل میگردد. با توجه به اینکه در وسط سیم پیچ کوره جسم هادی مانند فولاد چدن یا سایر فلزات قرار گیرد میدان مغناطیسی ایجاد گردیده باعث القا جریان های گردابی در این اجسام میگردد و این جریان های القایی جسم را گرم نموده و تا حد ذوب و احیانا تبخیر در کوره های (Coating) پیش میبرد با مانور روی فرکانس و قدرت کوره میتوان سیستم را جهت انواع کاربردها آماده نموده و در آن جهت به کار گرفت.
اجزای کوره القایی
به طور کلی قسمت های مختلف کوره القایی را میتوان به بوته، تاسیسات الکتریکی تقسیم بندی کرد.
الف) بوته
بوته حاوی اسکلت فلزی ،کوره ،کویل جداره ،نسوز هسته ترانسفورمر بوغها و پلات فرم است. به عبارت دیگر ،بوته محفظه ای استوانه ای از مواد نسوز است که در آن قراضه جهت عملیات ذوب ریخته میشود.
ب) تاسیسات الکتریکی
تاسیسات الکتریکی شامل تاسیسات خنک کن، تاسیسات حرکت ، بوته محل استقرار ،کوره تاسیسات تهویه، دژنکتور سکیونر ترانسفورماتور مبدل ،فرکانس خازن ها، چوک ها، کلیدهای کولر، مکنده ها و تابلوهای کنترل هستند.
انواع کوره القایی
کوره القایی از زمان اختراع تاکنون در شاخه های مختلفی مورد استفاده قرار گرفته شده است که بر حسب کاربرد و اندازه بسیار متفاوت ساخته شده اند. از یک کوره کوچک القایی در ابعاد یک کاسه کوچک تا یک کوره 40 تنی فولاد یا آلومینیومی متفاوت میباشد. میتوان کوره القایی را از نظر کاربرد به چند گروه عمده تقسیم نمود.
- کورههای آزمایشگاهی
کوره در ابعاد بسیار کوچک، که جهت مذاب کردن چند گرم فلز برای استفاده در ازمایشگاه ها و یا صنایع تزیینی مثل طلا سازی ها بکار میروند.
- کوره های نرم کننده در ابعاد کارگاهی
کوره هایی با ابعاد کوچک و بعضا متوسط که تا وزن چند کیلو برای گرم کردن فلز و تغییر حالت و ایجاد محصولات جدید به حسب نوع فلز مورد مصرف استفاده میگردد بطور مثال برای تغییر شکل و ایجاد وسایل تزیینی که با حرارت نرم و قابل انعطاف میگردند.
- کوره القایی در ابعاد صنعتی
کوره های با ابعاد بسیار بزرگ می باشد که برای گرم کردن چند تن فلز و تولید فولاد به کار برده می شوند.
انواع کوره القایی از نظر هسته و عملکرد
کوره القایی از نظر هسته به دو نوع کلی تقسیم بندی میگردد که با توجه به تغییر اساسی در تکنولوژی هر کدام میتوان آنها را در دو شاخه کاملا مجزا در نظر گرفت.
- کوره القایی هسته دار یا کانالی
کوره های القایی کانالی در گذشته عموما برای نگهداری فلز مذاب در یک دمای مشخص کاربرد داشته اند، اما امروزه گاهی اوقات برای ذوب فلزات نیز به کار می روند. این کوره شامل سلف به عنوان منبع توان و تولید انرژی است که از چندین رشته کلاف که توسط آب خنک میشوند تشکیل شده است. این کوره ها تلاطم سطحی کمتری در بوته نگهداری فلز مذاب دارند، در نتیجه خروج گاز مواد فرار با مشکل مواجه میشود. لذا جهت عملیات ذوب، کوره القایی بی هسته ترجیح داده میشود و کوره کانالی بیشتر به منظور نگهداری فلز مذاب در یک دمای مشخص مورد استفاده قرار میگیرد. در حالی که کوره های ذوب القایی کانالی دارای فرکانس خطی هستند، کوره های بدون هسته میتوانند از هر سه نوع فرکانس شبکه، متوسط و بالا باشد.
- کوره القایی بی هسته
کوره های القایی بی هسته، مدرن ترین و پرکاربردترین کوره های تولید فولاد به روش القا هستند که دارای یک سیم پیچ خالی هستند که در آن آب نقش خنک کننده را ایفا می کند و یک بوته که مواد مذاب و شارژ فلزی در آن القا و مستقیما ذوب میگردد.
تولید فولاد در کوره القایی بدون هسته فلز، درون یک پوشش نسوز که به وسیله کلاف احاطه شده است نگهداری میشود. در این حالت کوره ذوب القایی مشابه یک ترانسفورماتور است که فلز مانند یک کلاف ثانویه در ترانسفورماتور عمل میکند و با اعمال نیرو به کلاف اولیه احاطه کننده فلز جریان های گردابی القا شده و تولید حرارت میکند پس از ذوب فلز هم زدن و همگن سازی به طور طبیعی و در اثر وجود نیروها و جریان های الکترومغناطیسی اتفاق میافتد با انتخاب دقیق فرکانس و نیرو میتوان سرعت ذوب و همگن سازی را کنترل کرد.
انواع کوره القایی از نظر فرکانس
کوره های القایی را از نظر فرکانس میتوان به صورت زیر تقسیم بندی کرد:
- کوره های القایی با فرکانس پایین
چنانچه از نام آن پیداست این فرکانس همان فرکانس شبکه است. استفاده از فرکانس شبکه ارزانترین راه برای نصب کوره بدون هسته میباشد در این حالت به وجود مبدل فرکانس نیازی نیست. برای بار کوره فقط یک ترانسفورماتور مورد نیاز میباشد ترانسفورماتوری که در آن هسته ها از نظر مغناطیسی به حد اشباع درآمده اند یک جریان متغیر تولید میکند که شامل نوسانات زیادی میباشد. چنین کوره هایی با ۳ تا ۹ برابر فرکانس شبکه کار میکنند باید در کویل اولیه یک فیلتر هارمونیک کار گذاشته شود تا از بازگشت نوسانات به برق شبکه جلوگیری بعمل آید کویل هایی که بصورت متوالی با سیم پیچ های اولیه قرار گرفته اند این فیلتر را تقویت میکنند کوره هایی که با فرکانس پائین کار میکنند نیازی به دستگاه تنظیم بار ندارند چون بار به محض ورود به طور مساوی بین سه فاز تقسیم میشود.
کوره القایی با فرکانس پایین به دلیل بی نیازی از مولد یا ژنراتور با فرکانس بالا و در نتیجه پایین بودن قیمت اولیه آن به طور وسیعی در صنایع ریخته گری به کار میروند. کوره القایی فرکانس پایین دارای دو جفت کویل مسی القایی میباشد و ظرفیت آنها حدود ۱۰۰ تا ۲۵۰۰ کیلوگرم آلومینیوم میباشد. سیم پیچ های کویل مسی که در آنها آب جریان دارد مهمترین عامل انتقال الکتریسیته به حرارت میباشد. در کوره القایی بخصوص در انواع آن که با فرکانس پایین کار میکنند همواره لازم است در بوته مقداری مذاب نگهداری گردد تا در مراحل افزودن شارژ جامد به مذاب شارژ با سرعت زیادی انجام گیرد، اصولا هنگامی کوره القایی فرکانس پایین را خالی از مذاب میکنند که نیاز به تعمیر داشته باشد.
در کوره القایی فرکانس پایین چون فرکانس پایین است باعث افزایش تلاطم در مذاب میگردد. به طور کلی هر چه فرکانس کاهش یابد تلاطم افزایش مییابد به همین جهت افزایش شارژ و مواد کمکی در کوره القایی فرکانس پایین به سهولت انجام میگیرد. در نتیجه کوره القایی فرکانس پایین را میتوان برای ذوب و نگهداری مذاب و افزایش فوق ذوب استفاده نمود.
- کوره های القایی با فرکانس متوسط
فرکانس برق القا شده در این کوره ها بین ۵۰۰ الی ۱۰۰۰ هرتز میباشد بنابراین دارای هزینه سرمایه گذاری اولیه بیشتری نسبت به کوره های با فرکانس شبکه بوده است کار با این کوره ها ساده بوده و سرعت ذوب آن زیاد میباشد. تولید فولاد با کوره القایی را میتوان بدون نیاز به مذاب اولیه از حالت سرد بکار انداخت.
- کوره های القایی با فرکانس بالا
در فرکانس ۱۰۰۰ هرتز و بالاتر معمولاً از اصطلاح فرکانس زیاد استفاده میشود. برق از یک منبع سه فاز تأمین میشود. کوره القایی با فرکانس بالا معمولا شامل یک ژنراتور به قدرت ۵ تا ۱۰۰۰ کیلو وات است که فرکانس معمولی را به ۱۰۰۰۰ میرساند. اصول کلی ساخت کوره القایی با کوره القایی فرکانس کم تفاوت چندانی نمیکند جز آنکه برای تامین انرژی و فرکانس به ژنراتورها و ترانسفورماتورهای قوی نیاز دارد و ظرفیت آنها کم و محدود میباشد و حداکثر از ۳۵ کیلوگرم الومینیوم تجاوز نمیکند. کوره القایی با فرکانس بالا معمولا از سیستم یک فاز تغذیه میشوند و یک خازن و ژنراتور برای عرضه راندمان انرژی در سیستم ۳ فاز در آنها بکار گرفته میشود. بوته ها و مواد نسوز در داخل کوره القایی بایستی دو پارامتر متضاد را شامل شوند اول آنکه برای انتقال جریان و القاء ان نازک و از قابلیت انتقال برخوردار باشند و دوم آنکه به اندازه کافی ضخامت داشته باشند تا از استحکام زیاد برخوردار باشند که معمولا این ضخامت را ۸ درصد قطر بوته منظور میکنند.
- کوره های القایی با فرکانس متعدد
این نوع کوره ها معمولا دارای سه فرکانس متفاوت بوده و دارای مزایای هر دو کوره القائی با فرکانس شبکه و متوسط میباشد. استفاده از این کوره ها برای کارگاه های ریخته گری کوچک و متوسط مناسب است.
جمع بندی تولید فولاد با کوره القایی
تولید فولاد با کوره القایی کوره القایی در مقایسه با کورههای سوخت فسیلی دارای مزایای فراوانی از جمله دقت بیشتر تمیزی و تلفات گرمایی کمتر است. همچنین در کوره هایی که در آنها از روش های دیگر غیر القاء استفاده میشود. اندازه کوره القایی بسیار بزرگ بوده و زمان راه اندازی و خاموش کردن آنها طولانی است. کوره القایی از نظر افزایش و تقلیل مصرف انرژی نسبت به سایر کوره ها دارای مزایای فراوانی میباشد. این کوره ها در ظرفیت های مختلف قادر به ذوب از ۱۵ کیلوگرم تا چندین تن میباشد.
در کوره القایی هیچ گونه فعل و انفعالی شیمیایی که باعث افزایش ناخالصی و تغییرات ترکیبی مذاب گردد انجام نمیشود و علاوه بر آن به دلیل عدم استفاده از الکترود نسبت به کورههای قوس الکتریک امکان ورود ناخالصی های مواد از طریق مکانیکی نیز امکان پذیر نیست و از نظر توزیع حرارت و کنترل ترکیب مطلوب میباشد و از نظر مسائل الکتریکی محدودیتی برای افزایش درجه حرارت ندارند.
تهران القا تولیدکننده کوره القایی است که با پشتوانه علمی و فنی خود به طراحی، تولید و ساخت انواع کوره القایی با توان 10 الی 250 کیلو وات و فرکانس 10 الی 120 کیلو هرتز می پردازد.